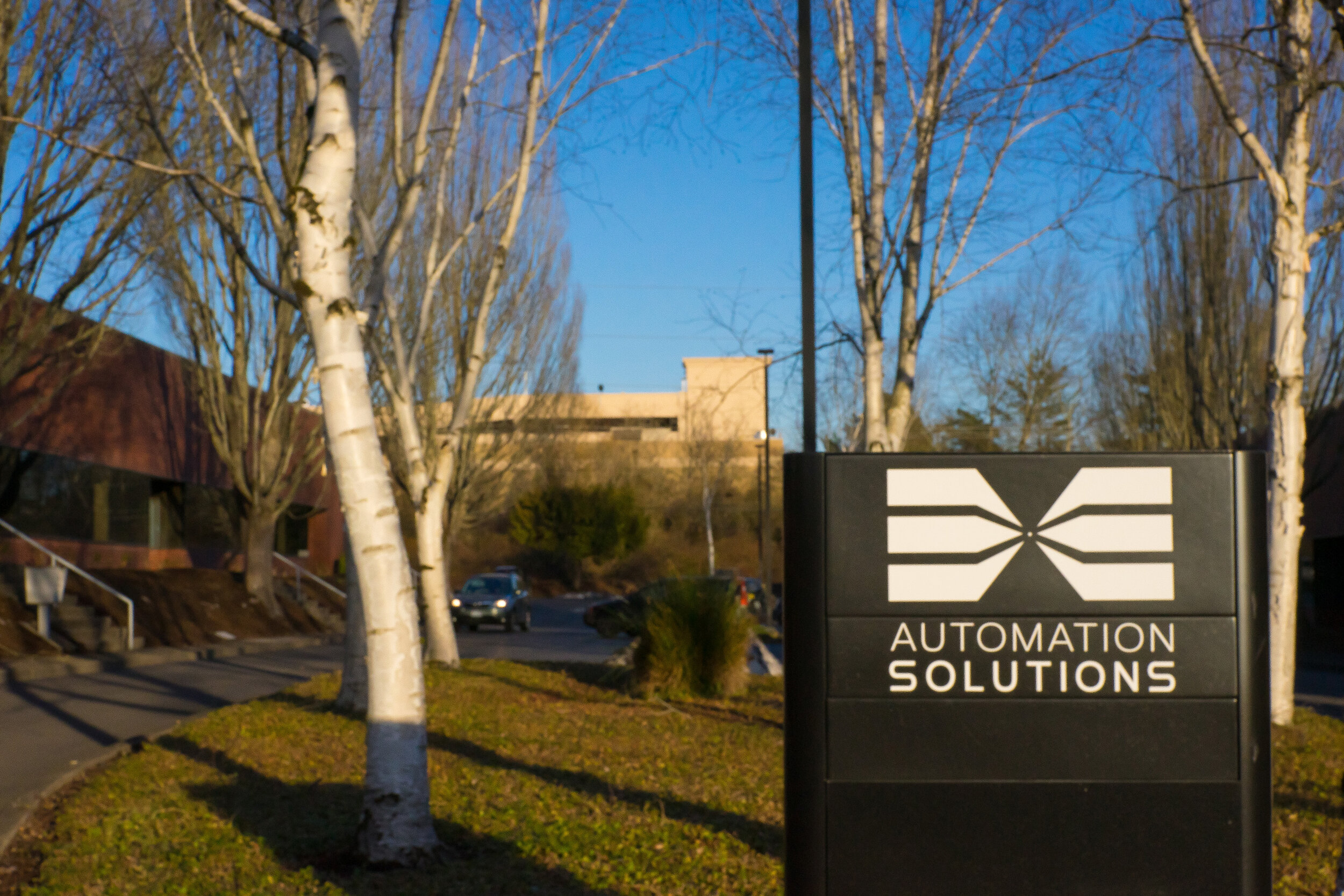
LEADING MANUFACTURER OF SILICON WAFERS REVIVES ITS DATED BANDSAW MACHINES WITH SERVO UPGRADES, VFD REPLACEMENT AND UPDATED PROGRAMMING
Band saws are used to slice silicon ingots into thin wafers, which are the basic building blocks of semiconductor devices.
Challenge:
A leading silicon wafer manufacturer faced a major obstacle - their aging band saws, vital to their process, were experiencing frequent failures and excessive downtime due to worn-out components. Critical spare parts were dwindling, the original manufacturer offered lengthy lead times (read 2-3 years to get essential spares), and replacement machines meant costly redesign of the entire process flow and production downtime.
Solution:
Automation Solutions restored these machines and the customer’s productivity. . Instead of opting for a complete overhaul, they chose a strategic approach:
Replacing key components: The obsolete servo controllers, servo motors and VFDs, the culprit behind breakdowns, were replaced with current generation alternatives. This not only revived the machines but also secured readily available spare parts for the future.
Resurrecting with precision: While developing the upgrade path the team discovered a flaw in the current machine design. - the readouts for the motor that controls the slant of the bandsaw blade was inaccurate.and would vary machine to machine.. Through meticulous analysis and the newer capabilities of the replacement servo amplifiers, they designed a replacement monitor that would display the angle of the blade to the third decimal point, significantly reducing rejections and optimizing output.
Cost-effective revival: By revitalizing the existing machines, Automation Solution saved the client substantial costs compared to purchasing new equipment. They saved their client the expense of new machines while resolving the current production bottle-neck. Automation Solutions was also able to break up the renewal process into multiple installs which minimizes the customer’s production impacts during the machines down-time for the renewals.
Results:
Extended lifespan: The band saws received a new lease on life, postponing the inevitable transition to new machines.
Readily available spares: Access to readily available replacement parts ensures smooth operation and eliminates dependence on long lead times.
Cost savings: By avoiding a new machine purchase and its associated complexities with machines, the client significantly reduced their capital expenditure.
Time saved: Minimizing downtime prevented potential lost business and kept customers happy.
The revitalized band saw machines brought a wave of benefits:
Conclusion:
Automation Solutions intervention is a testament to the power of ingenuity and precision engineering. They not only breathed new life into aging equipment but also saved the client valuable time and resources, proving that sometimes, the best solution lies in resurrecting the past with a touch of the future.
Ready to revitalize your aging equipment and boost productivity?
Schedule a free consultation with Automation Solutions today and discover how we can customize a cost-effective upgrade plan for your specific needs.